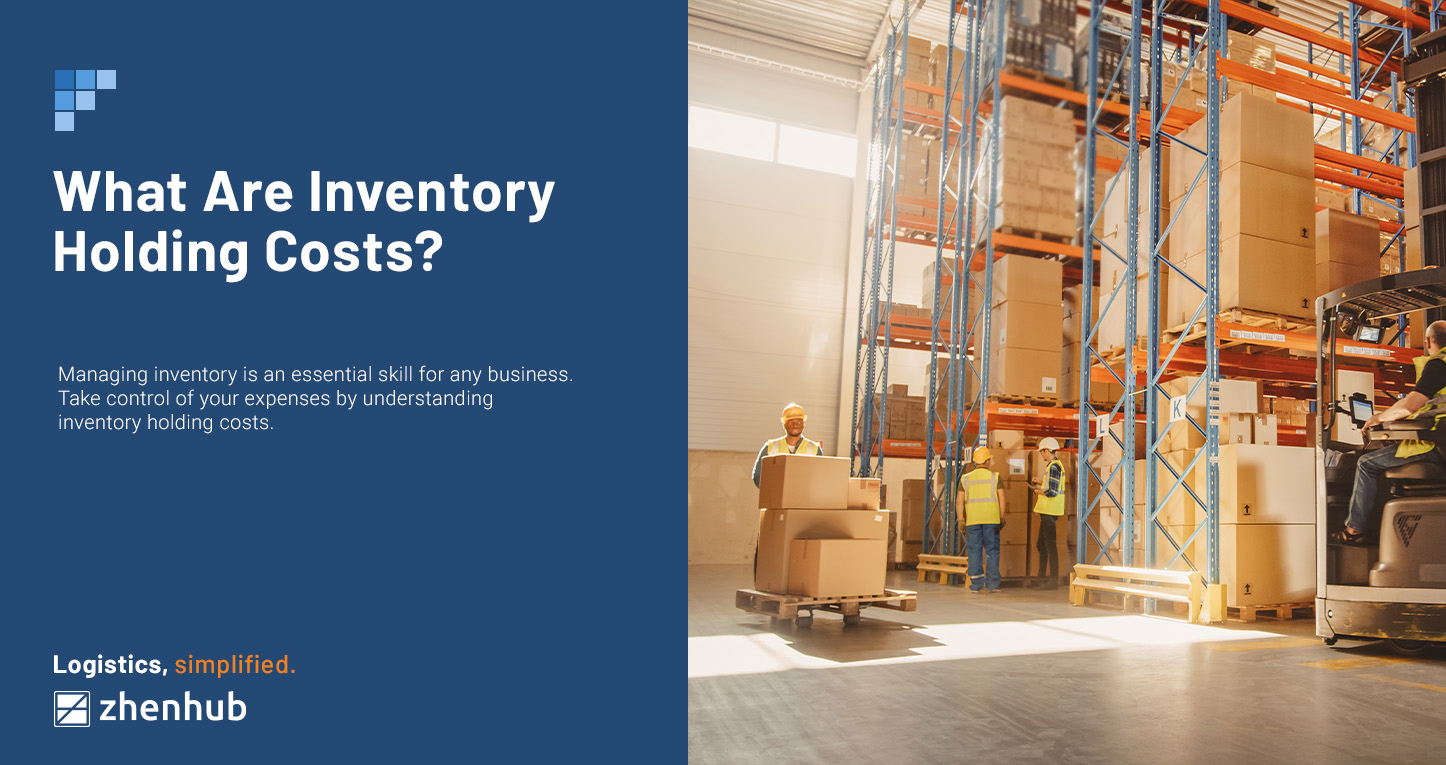
What Are Inventory Holding Costs?
Time to read: 5 minutes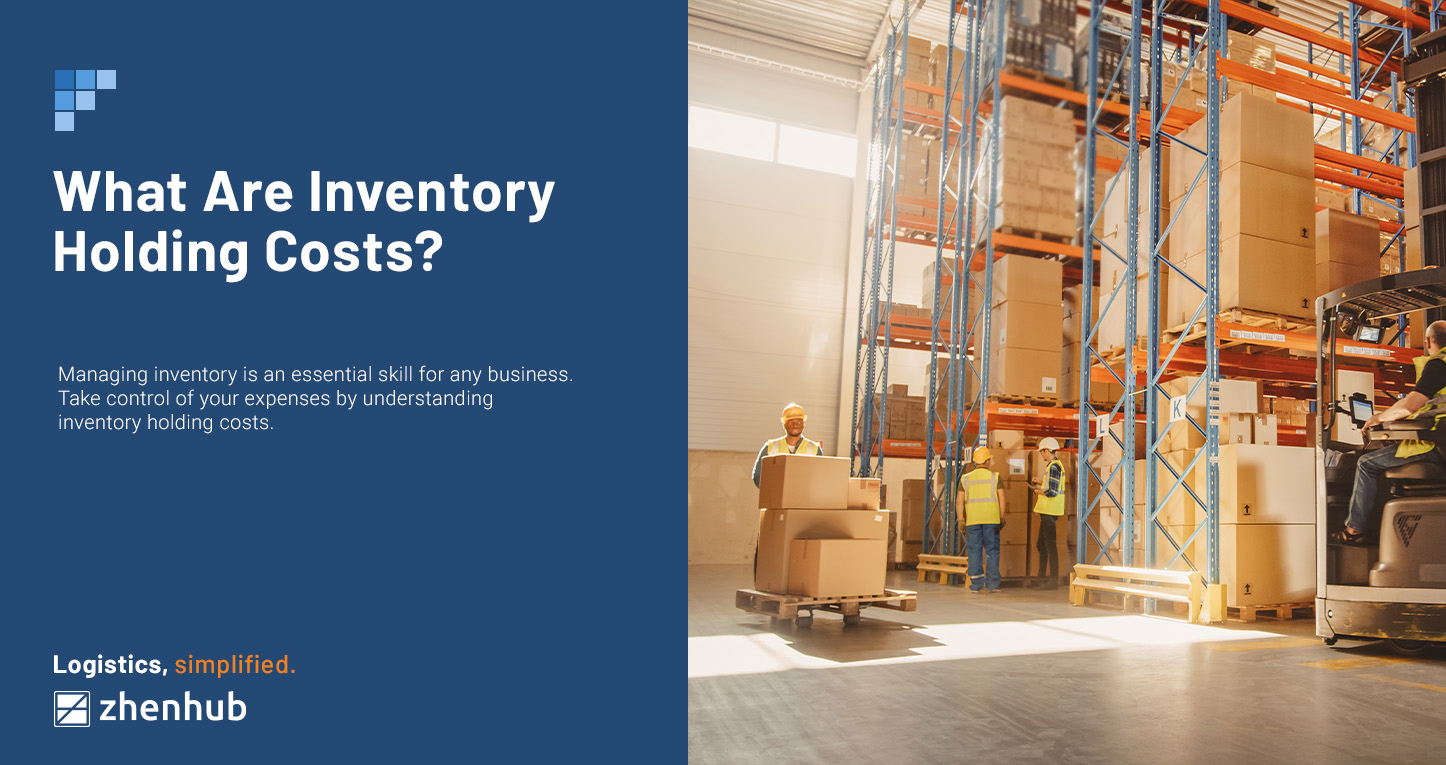
Increasing revenue is almost always the greatest priority of many business owners. However, solely focusing on this can lead to an oversight of less evident costs and hurt their overall profitability. Inventory holding costs, or the costs associated with keeping inventory until sold, are among the most costly “hidden” expenses.
The expenses incurred by keeping unsold items in storage are known as holding charges or inventory holding costs. Together with ordering and shortage costs, these costs make up a portion of the overall inventory cost.
The cost of damaged or spoilt goods, storage space, labor, and insurance, are all included in a company’s holding expenses. Just how big can this cost? Inventory with accounts receivable and accounts payable could tie up $1.1 trillion in cash.
While this is an unavoidable aspect of running an eCommerce business, it is also extremely crucial. You might get overcharged if you’re not careful or don’t know how to manage storage and inventory turnover. It can be caused by a storage solution that doesn’t have a clear price schedule, or your inventory projections didn’t go as planned.
Businesses must consider implementing demand planning and forecasting as these prices rise and fall. Modern logistics technologies can help enterprises keep the right quantity of stock.
4 Components of Inventory Holding Costs
Your inventory holding costs are capital, storage, service, and inventory risk costs. Your finances can be solid and more controlled if you know how each one impacts your cost of goods sold (COGS).
These groupings serve to divide the wide range of inventory costs that exist roughly.
1. Capital Costs
The cost of capital, which often makes up the largest percentage of inventory holding costs, consists of the product purchase price plus any interest and additional charges. It’s evident if your company took loans to buy goods.
2. Storage Costs
Storage costs are expenses to keep your stock stored safely in specific locations, such as your warehouse. There are two parts to it: fixed costs and variable costs.
Variable costs include staffing, material handling charges, and utilities related to the facility. Fixed costs for the storage space include rent or mortgage payments.
3. Service Costs
Service fees keep your inventory safe from issues like theft or workplace accidents. You may also need to pay fees to ensure that legal requirements are met and to maintain inventory management software systems. Examples include insurance premiums, inventory taxes, and software licensing fees related to storing inventory.
4. Inventory Risk Cost
A certain amount of risk is involved in carrying inventory, and this risk has a financial impact. Several things make up this cost element. The risk of shrinkage is any inventory loss after an item is acquired before you sell it to your clients. Shrinkage can also happen due to administrative mistakes, staff theft, or transit damage.
The decrease in your product’s value while in storage is another risk. The release of newer goods or models is one of the potential causes for this. Thirdly, you risk obsolescence when you keep items after it’s passed their sell-by or expiration dates.
Calculating for Inventory Holding Costs
Calculating inventory holding costs will help determine how much money you make from your stock. It’ll also prevent losses that can result from keeping it for too long. Your holding expenses are determined by dividing the holding amount by the entire value of your inventory and multiplying the result by 100.
Inventory Holding Cost (%) = Total Inventory Holding Sum ÷ Total Inventory Value x 100
First, you must determine your service, capital, storage space, and risk costs.
Inventory holding sum = service cost + capital cost + storage space cost + inventory risk
Next, figure out how much-unsold merchandise you have in a warehouse or storage facility and how much it is all worth.
Divide the holding amount by the entire worth of your inventory, which you calculated in the previous step. After that, divide this sum by 100 to obtain a percentage.
For example:
You own an electronics company that stores its unsold inventory in a warehouse. The total value of your inventory amounts to $500,000. Your inventory service, capital, storage space costs, and inventory risks amount to $70,000. Using this information, you can calculate your holding costs as follows:
Inventory holding sum = $70,000
(Inventory holding sum / total value of inventory) x 100 = holding costs (%)
($70,000 / $500,000) x 100 = holding costs (%)
14% = holding costs
Therefore, your electronics company incurs a holding cost of 14% of its total inventory value.
Inventory holding costs can impact a company’s overall financial health because they may account for one-quarter of total inventory expenditures. Your organization could have cash flow issues if it didn’t quantify the cost of maintaining goods, such as by using an inventory or stock control system.
Business leaders may pass up a lucrative investment or expansion opportunity because it has too much cash locked up in inventory, all without being aware of how much carrying costs are hindering the company’s growth.
4 Ways to Reduce Your Inventory Holding Costs
The long-term viability of your company depends on finding an inventory storage solution with reasonable holding costs. Yet, your company’s cheapest storage option isn’t necessarily the best option. To put it another way, what works well for one firm won’t always work for another.
Companies that take advantage of bulk discounts increase holding costs since they store huge quantities for a long time. In contrast, a company using the lean model will keep a small amount of inventory on hand, which results in lower holding costs.
Here are some best practices that can help reduce your overall expenditure on holding costs:
1. Optimize Your Storage Space
Start by making changes to the storage space’s layout. Don’t underestimate the value of good design. Changing your storage room’s architecture could give you more space and save carrying expenses. Consider making adjustments like decreasing the equipment handling aisle. Add a mezzanine level, rearrange your storage area, or switch to more suitable storage modes. Investing in robotics for warehousing can make
2. Avoid Keeping Too Much Inventor
Following a set of inventory key performance indicators (KPIs) will allow you to assess each product in your stores or the warehouse. You’ll also have more data to calculate the right amount to stock up on.
Accurate forecasting is essential. But so is software that notifies customers when it’s time to place another order and offers recommendations for how much to buy. Finding the ideal balance will take time and trial and error, but the savings from optimal inventory levels make it worthwhile.
3. Invest In Inventory Management Software
Consider implementing online inventory management strategies that reduce carrying costs, back ordering part of your items or consignment sales. Use inventory management software to lower your carrying costs rather than relying on excel spreadsheets. Manually recording every transaction is tedious, therefore becoming error-prone and time-consuming. The inventory control software will give helpful information, such as precise demand projections and reorder points.
Using a warehouse management system (WMS) may expedite and reduce the cost of shipment and fulfillment.
4. Negotiate Flexible Terms with Suppliers and Customers
Renegotiating contracts with your suppliers and customers is another way to keep holding costs down. Before clients purchase your products, be sure you don’t bear all the risks and expenses. Structure contracts with suppliers, for instance, such that they are liable for theft, damage, or other expenses while the products are in their care.
Distributors and manufacturers should look for ways to reduce their carrying costs. For instance, to collect part of those carrying expenses, include a maximum holding time for inventory in the contract and add penalties for each additional day.
You risk taking on big losses by selling a sought-after item at an unprofitable price if you don’t base your price decisions on total inventory holding costs. The overall status of inventory is what inventory management focuses on. Make sure you have the right stock on hand, optimize the ordering procedure, and detect out-of-date goods.
Although the idea of inventory holding cost is not particularly interesting, it is crucial to your company’s success.
It’s a significant number since it indicates how long your firm can maintain its inventory before it starts to lose money on unsellable products. It also demonstrates how much you must sell and acquire to keep the right amount of stock. Understanding holding costs and reducing costs may a business recover money held in inventory and boost earnings.
With ZhenHub, our logistics software solutions are optimized for eCommerce operations. Get real-time insight into the stock movement and complete control over your inventory. Optimizing your inventory holding costs has never been easier. Sign up now to experience our all-in-one logistics platform.