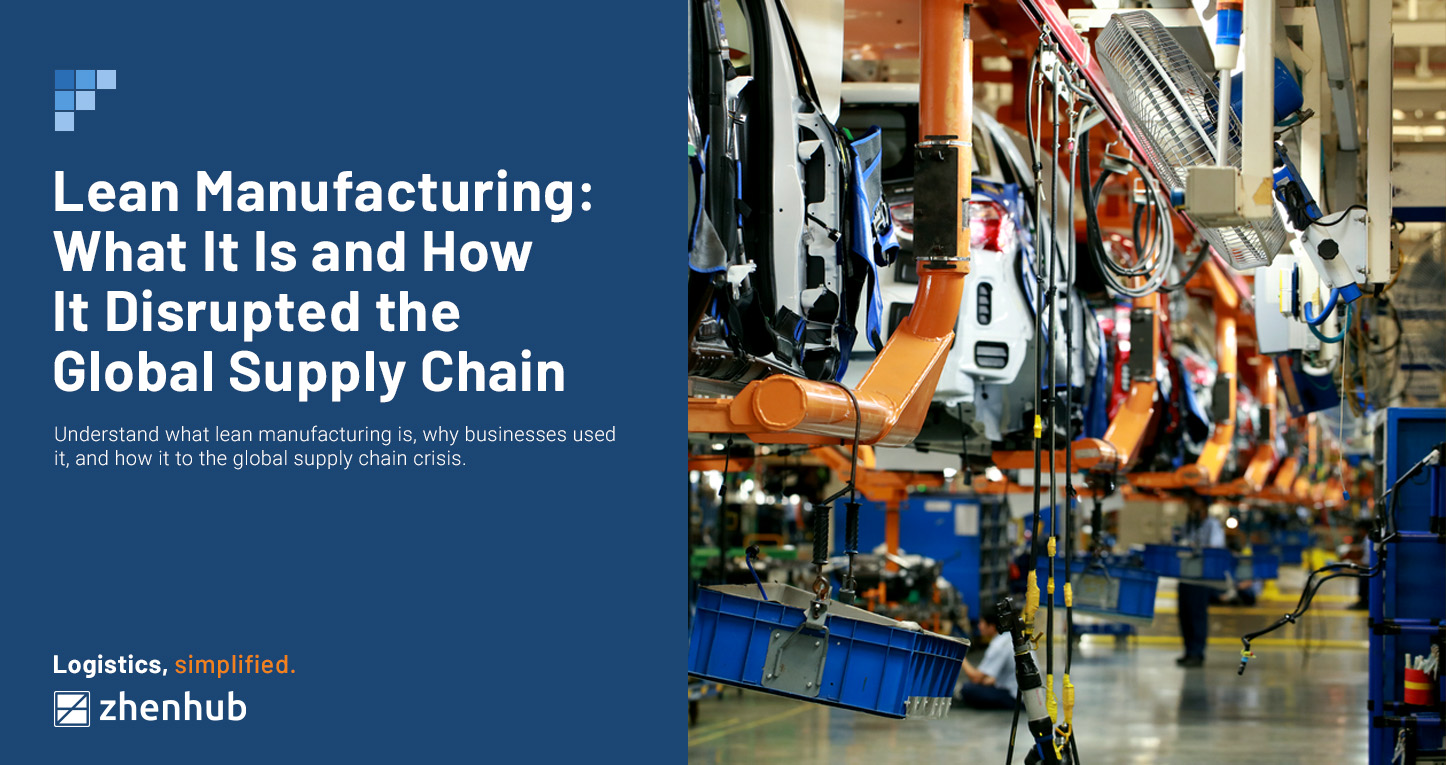
Lean Manufacturing: What It Is and How It Disrupted the Global Supply Chain
Time to read: 5 minutes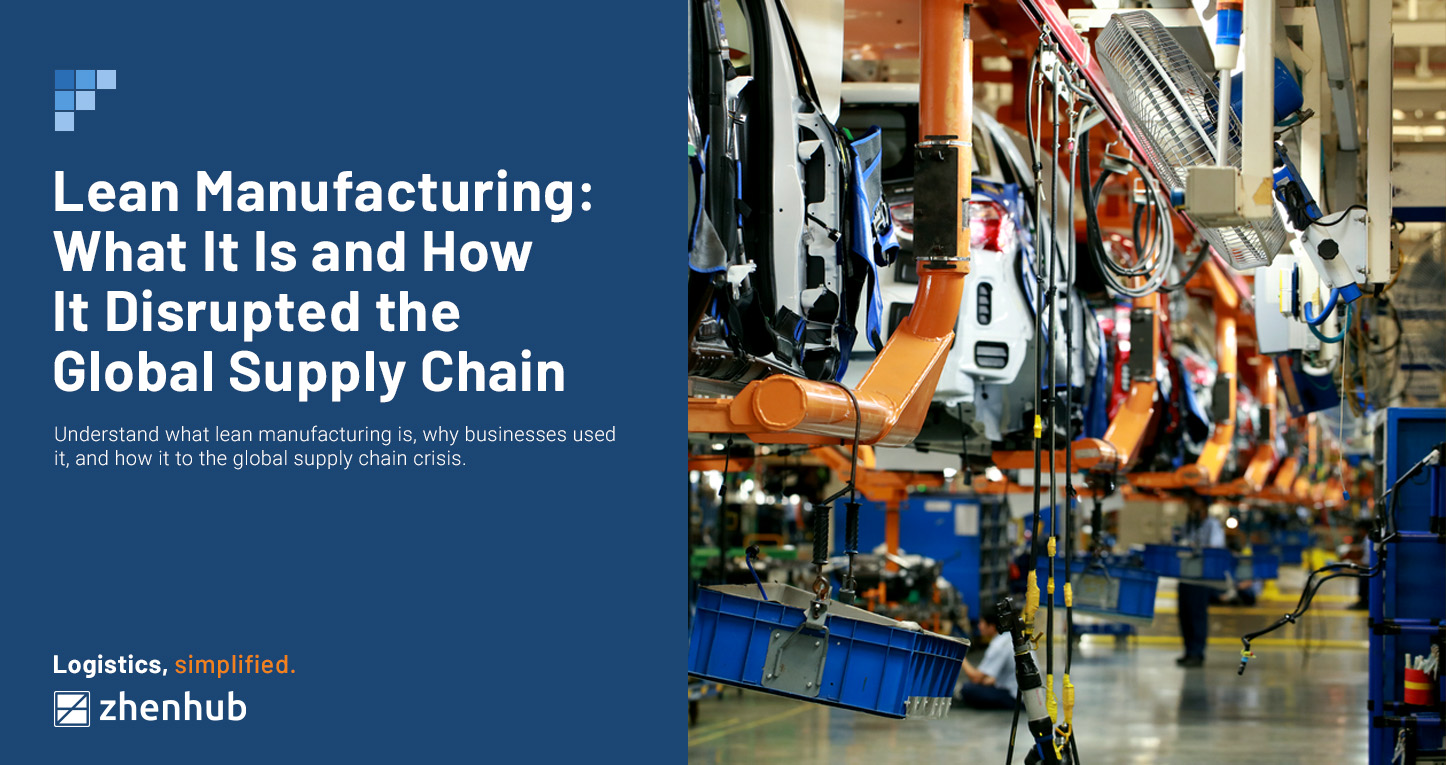
Lean manufacturing is considered a practical production philosophy aimed at minimizing waste and increasing production. It has been a boon for most companies in the past, but the pandemic turned it into a hindrance to business recovery. It has even significantly contributed to the global supply chain crisis.
The benefits are hard to pass up: reduced lead times, operating costs, and improved product quality by focusing on processes that create more value for your customers. By relying on accurate demand forecasting and streamlined production, inventories get stocked only when needed.
How could this manufacturing method affect the worldwide production and distribution problems? How can businesses adjust their strategies to deal with this? Discover the history of lean manufacturing and what other innovative techniques you can implement to manage your supply chain better.
The Definition and Origins of Lean Manufacturing
Lean manufacturing is streamlining processes and procedures to eliminate waste and maximize productivity. Waste, in this case, does not refer to trash or byproducts of manufacturing — it’s the downtime. Companies aren’t maximizing available resources, leading to inefficient processes and lost production time. Examples of this can be idle workers, too much inventory, or skills that don’t create value for customers.
The idea of lean production has been around for centuries, but Benjamin Franklin brought up the idea of reducing waste in his yearly almanac, “Poor Richard’s Almanack.” He explained to his readers that avoiding unnecessary costs could bring home more profit instead of increasing sales.
Frederick Winslow Taylor further explored this idea, a mechanical engineer who wrote in his 1911 book entitled “Principles of Scientific Management”: “whenever a workman proposes an improvement, it should be the policy of the management to make a careful analysis of the new method, and if necessary conduct a series of experiments to determine accurately the relative merit of the new suggestion and the old standard. And whenever the new method is found to be markedly superior to the old, it should be adopted as the standard for the whole establishment.”
Influential American industrialists, such as automotive magnate Henry Ford, saw lean production as a means to counter the competition of cheaper offshore labor. Lean manufacturing would be codified best by two chief engineers at the Toyota Motor Corporation, Shigeo Shingo and Taiichi Ohno. Ohno formed the Toyota Production System (TPS) to revolutionize the car maker’s manufacturing processes.
This system resulted from a long process of studying every step of their production process and researching multiple improvement teams. Coming from the post-war period of the 1940s and left with a depleted Japanese economy, Ohno looked at actual sales to determine their working schedules instead of basing them on production targets. Toyota would avoid overproduction, which also meant fewer costs overall. They adopted a “build-to-order” scheduling system, which would later be more widely known as “just-in-time” manufacturing (JIT).
The TPS lays out five core principles that help companies to understand lean. These are:
- Value
What does your customer consider to be important? What are they looking for, and how much are they willing to pay for a product or service? You should be able to provide this value by using what is only necessary.
- Value Stream Mapping
Companies should have an overview of the entire production process and analyze everything involved. It’ll allow organizations to evaluate which changes can improve parts of the process and what steps to remove to eliminate waste.
- Create Flow
Improving lead times through streamlined processes and minimal delays.
- The Pull System
Work is only done when there is a demand for your products or service. Flexibility, communication, and efficient processes are vital to meeting needs and starting new work on time.
- Perfection through Continuous Improvement
Continuous assessments and timely improvements can bring about the constant elimination of waste. All staff members and workers have to be transparent to foster a sense of responsibility regarding their work.
Initially, there are seven different types of waste were also laid out by the TPS as the following:
- Unnecessary transportation
- Excess inventory
- Unnecessary movement of people, equipment, or machinery
- Waiting – either people or idle equipment
- Over-production of a product
- Over-processing or adding unnecessary features to a product
- Defects that require costly correction
Modern proponents of lean manufacturing have since added an eighth type of waste: “unused talent and ingenuity.” This waste refers to the neglect of feedback by employees, which can identify possible roadblocks and lead to process improvements.
To summarize, these wastes have been categorized into three different categories using Japanese phrases:
- Mura
It’s the unevenness or waste as a result of fluctuating demand. This can be caused by customer preferences or new products and services introduced by a company that demands additional work.
- Muri
Overburden or waste due to trying to do too much. It’s influenced by poor resource allocation. When work is not correctly assigned and managed, staff waste too much time by switching between tasks which can cause burnout and affect actual work quality.
- Muda
Processes or work that does not provide any value to your customer. If it doesn’t support or enhance any part of your process, then it should be up for elimination in your value mapping stream.
How Did Lean Manufacturing Contribute to the Global Supply Chain Crisis?
The supply chain crisis in 2022 has been characterized by shortages, delays, port congestion, and rising prices. The idea of JIT is a major cause with production lines being unable to cope with a massive increase in demand. With a focus on only providing what is needed on a tight schedule, the sudden surge of demand has left companies struggling to provide the correct value to their customers.
Inventories got quickly wiped out since they could not accommodate the increase in orders. A Lean supply chain was inadequate in generating a buffer for sudden economic changes. Case in point: the global COVD 19 pandemic. It impacted many industries, such as medical equipment and food. These sectors couldn’t adequately meet consumer demands during lockdowns. In addition, the pursuit of eliminating waste influenced many businesses to avoid overstocking, therefore putting themselves at risk of not having enough products to sell.
Inventories that have become too lean responded poorly to unpredictability. Just-in-time works on anticipating “optimistic” levels of demand. Various risk factors can interfere with the cost-effective and efficient method of providing products and services when customers need them the most.
Lessons to Learn from Lean Manufacturing
It would be unfair to blame lean processes. Many factors have caused the current supply chain crisis. Worker shortages and a lack of space for unloading have led to delays for retailers receiving their items from shipping containers. Stockpiling isn’t a clear-cut solution, which leads to high holding costs.
If anything, the pandemic has exposed weaknesses in the supply chain, companies that have stretched themselves too thin to prioritize short-term gain instead of long-term stability. The TPS was born out of the need to work around shortages and lack of materials, as Toyota operated in a Japanese economy ravaged by World War II. Unfortunately, lean thinking may have become a victim of its benefits; many companies seek to enjoy streamlined processes without properly implementing its guiding principles.
While lean logistics is not perfect, it’s the idea that getting the most value out of every piece and part of your process can go a long way. Waste is never a good thing and will always be a negative for a business.
Outsourcing your logistics and leveraging emergent technologies that power digital warehouses are cost-efficient options for streamlining processes. It also gives companies transparency to pinpoint shortages quickly. Data gathering and forecasting are more crucial than ever. Investing in the right technology and software will help your business become more resilient and flexible and provide the foundation to scale.
Having the ability to source from multiple manufacturers and vendors can be a complex task; however, automation can help. In addition, diversity from other regions will help mitigate a sudden rise in demands as your business will have the flexibility to compensate. Being able to spread your risk, making it more manageable, and giving yourself more options to deal with problems is a great way to weather unforeseen circumstances.
Lean thinking still has great value today, despite being commonly seen as contributing to the global supply crisis. It can help businesses evaluate how to run their businesses better and that complex methods aren’t a one-size fit solution. Keeping up with demand and identifying value where you can find it strengthens your business for the future. The right mindset is key to achieving long-term success instead of trying to copy successful strategies that have worked for others.
ZhenHub offers a complete suite of digital logistics solutions. We can help streamline your fulfillment by providing superior value to your business process to achieve customer satisfaction. Contact us or sign up to discover the different ways we can accelerate your growth and help you achieve a leaner business.