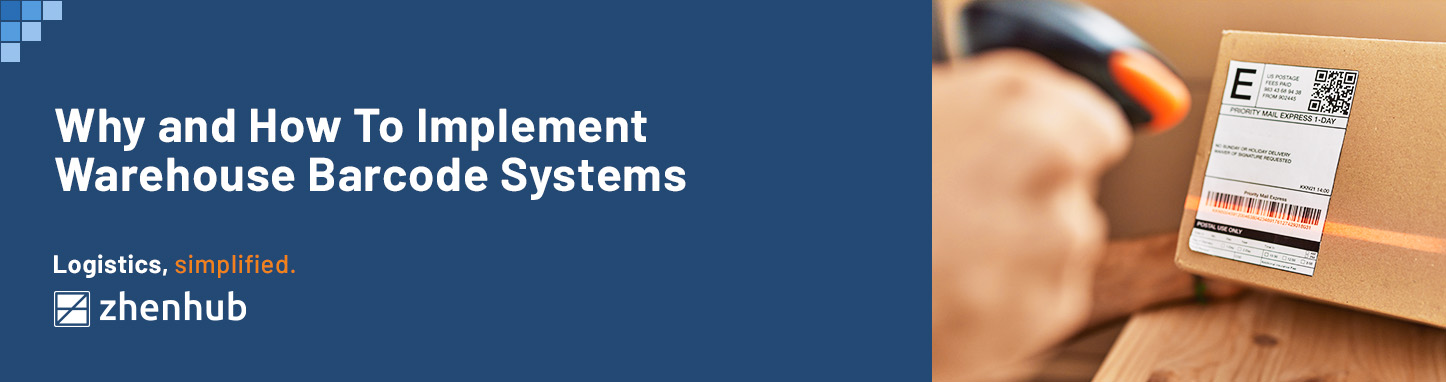
Why and How To Implement Warehouse Barcode Systems
Time to read: 7 minutes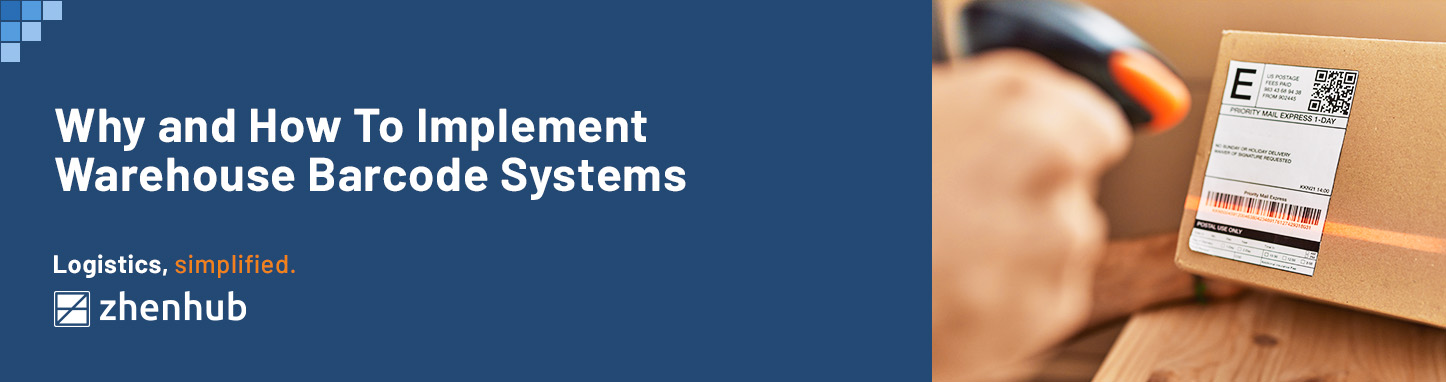
Many eCommerce retailers, when starting, will opt to go with a manual stock-picking procedure. The process is simple: you go to where the item is typically kept and pick it up when an order is received. It’s easy to do and keep track of when you only have a small inventory. But when your inventory gets more diverse, and your order volume increases, this approach can become tedious, slow, and prone to errors. Nowadays, it’s simple to make a mistake and send the wrong item to a customer. And errors like these never end well. You’ll likely be met with negative feedback, fewer sales, and less repeat business.
However, these issues with inventory management can easily be solved with computerized picking and warehouse barcode systems.
Warehouse barcoding has become an indispensable technique for optimizing inventory management. The growing complexity of global supply chains only highlights their importance.
Implementing warehouse barcode systems can significantly improve inventory management and order fulfillment accuracy and efficiency. Barcodes simplify processes and reduce errors by offering a standardized, automated product tracking and management method.
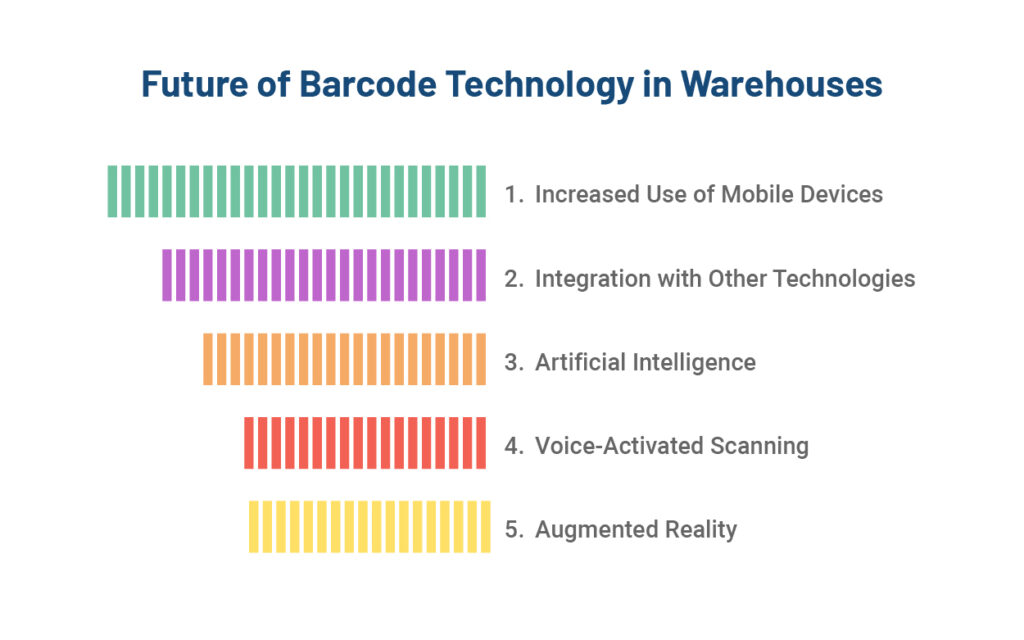
Barcode Technology: Enhancing Accuracy in Warehouse Receipts – FasterCapital
In a barcode inventory system, individual items are given a barcode. These are unique identifiers that contain specific data about a product. The barcode is scanned upon product sale, and the data is then transmitted to a central database.
This is helpful when processing online orders. When picking a product for fulfillment, the warehouse employee scans the barcode. The scanner immediately informs the workers if the correct item has been selected. Additionally, it logs the activity into your inventory management system, which aids in maintaining precise stock level tracking. These updates assist you in monitoring your inventory in real-time and enhancing picking accuracy and speed.
How Warehouse Barcode Systems Give You a Competitive Advantage
Understanding the fundamentals of barcode technology before exploring the advantages of warehouse barcode systems is essential. The most commonly used variants are one-dimensional (1D) and two-dimensional (2D) barcodes.
1D Barcodes
An informational picture that can be mechanically read and decoded is called a 1D barcode. A scanner, such as a laser beam, is used for reading and decoding. The scanner’s reading head reflects the code in the scanner, interpreting the data contained in the lines. Thus, the barcode may be considered the product’s unique identifying number.
EAN and UPC, two of the most well-known and conventional barcodes, are classified as 1D. Many retailers make use of both of these barcodes. Cross-border readability is ensured since both EAN and UPC adhere to an international standard.
Barcodes and Basic Warehouse Scanning (taskletfactory.com)
2D Barcodes
A 2D barcode holds up to 100 times as much information as a 1D barcode. It can also store sophisticated data, like links and images. 2D barcodes are usually simpler to read from a distance since they are always the same size. They are utilized for various purposes, such as app downloads, medical product labeling, and information exchange with customers via codes placed on city buses or standers. Only an Imager barcode scanner is capable of reading 2D barcodes. Because 2D scanning is not yet available for output boxes, it is not yet widely used in retail. You may recognize QR codes as a common form of 2D scanning.
Barcodes and Basic Warehouse Scanning (taskletfactory.com)
Inventory management requires the use of barcode scanners, which are devices that read barcodes that are created using barcode software. Barcodes may hold a wealth of data your inventory management system may utilize. A barcode, for instance, can transmit data about a product, such as its name, weight, measurements, and warehouse location.
Greater Accuracy
Barcode inventory systems minimize manual operations that are prone to human error. Avoid incorrect input into your inventory system, skipping lines, misreading numbers, or just having poor handwriting.
Faster Data Entry
Barcodes are scanned in seconds while your inventory software system swiftly and precisely interprets the signals. Workers who utilize barcode systems perform better than those who manually enter data alone. Productivity using barcodes is noted to result in 8 to 10-fold increases in efficiency.
Better Data Analysis
Complete data makes real-time reporting and more accurate inventory information possible. When inventory counts reach a certain level, you’ll get notifications telling you to place a replenishment order to satisfy customer or producer demands.
6 Best Practices to Implement Warehouse Barcode Systems
Installing a barcoding system in your warehouse might be a challenging task. But it’ll be easier to implement with the right preparation and research.
An eCommerce business relies on a distribution center. These locations see many goods and products moving around, entering, and exiting the facility. An efficient warehouse barcode system is needed to facilitate all these product movements.
A well-thought-out warehouse barcoding system helps to improve fulfillment speed and efficiency. You’ll also need well-trained and equipped staff to maximize the technology’s potential and limit mistakes and error potential.
1. Identify and Assess Your Warehouse Needs
Evaluating your warehouse’s needs and goals before the implementation process is essential. Think about the kinds of goods you deal with and how often they are moved. Identify the number of workers utilizing the warehouse barcode system and the software and equipment budget.
A review of your warehouse layout design may also be necessary. It’ll ensure your warehouse barcode system complements the facility’s overall architecture and operation. It will also help in selecting the appropriate systems and barcode placement locations. Remember that each item must have a distinct barcode number, a designated storage location, and a procedure for reviewing and scanning goods.
2. Select the Appropriate Label Technology
As discussed above, there are multiple types of barcode technology, each with its benefits. A 1D barcode is the most popular and economical form. They are often seen on retail items. A different choice is a 2D barcode, which uses black and white squares or dots to hold additional data. Meanwhile, 2D barcodes, such as those found in MaxiCodes and QR codes, are becoming increasingly popular.
Investing in radio-frequency identification (RFID) tags, which utilize radio waves to send real-time data, is another option if you want more sophisticated labeling. For daily accuracy, they are the fastest alternative, but the cost is typically higher. Ultimately, the technology you choose will depend on how well it fits your warehouse’s requirements and financial limits.
3. Invest in Supporting Hardware and Software
You will need hardware and software components to read data from labels to install a warehouse barcode system successfully. Platforms for asset and inventory management, including warehouse management systems (WMS), should be a priority. Select software that works in perfect harmony with your warehouse barcode system. You can handle orders, keep track of inventory, and streamline warehouse operations with it.
You’ll also need tools like label printers and—above all—warehouse barcode scanners. Barcodes may be scanned anywhere they are using these portable gadgets. Numerous types are available, and they may be used offline or online. Your physical and inventory demands will determine which solution is ideal, so pay attention to ergonomic and versatile alternatives.
4. Practical Barcode Design
Create a barcode system that combines your hardware, software, and label selections to fit your inventory management procedures and warehouse architecture. Consider data fields, label format, and label positioning. Your employees will get the best real-time picture of the facility if your warehouse barcode system is thoughtfully designed.
Pick a location for the labels so that scanning is simple. Next, decide on a format for your barcode labels. Ensure they have all the required information and that your whole facility adheres to a single, integrated standard. Choose the data fields for your barcodes, such as product IDs, descriptions, or quantities, depending on the program you’ll be using.
5. Comprehensive Staff Training
When your warehouse barcode system is operational, it’s time to teach your staff and ensure employees can easily understand the process. It’s essential to test your system thoroughly before use. Identify pain points and opportunities to train warehouse staff properly. Feedback will help improve the system’s functionality and data-gathering capability. It’ll also provide other improvements to maximize efficiency further.
Ensure the staff knows how to use barcode scanners, find and reliably scan barcodes, and resolve any potential problems independently. Sustained assistance and training are necessary to optimize the system’s advantages. Since barcodes may be customized for each warehouse, your employees must know the procedures in your particular setting.
6. Continuous Auditing and Inspection
Roll out your warehouse barcode system progressively throughout your business after you’re confident it’s operating as intended. Maintain a close eye on performance, assessing the system’s effectiveness and making adjustments as needed. As your operations grow, you might need to add more phases to the scanning process. Alternatively, you might discover that simplifying it would allow for quicker results.
Your chosen barcode system partners often provide inspection and troubleshooting services to assist you in resolving any potential problems.
Using warehouse barcoding can help improve your warehouse operations’ accuracy and efficiency and simplify inventory management. Employing a warehouse barcode system and using best practices will boost output, save labor costs, and enhance order accuracy.
Warehouse operations will depend increasingly on barcode technology as the supply chain changes. Keeping up with the most recent advancements in barcode technology and best practices can make your warehouse operations efficient and competitive.
ZhenHub helps optimize the performance of warehouse barcode systems. Integrate barcode technology with our inventory management systems. Get real-time updates on the go and manage multiple fulfillment centers at once. Sign up at our website for access to our logistics software. Contact our fulfillment experts to learn more about logistics software integrations.