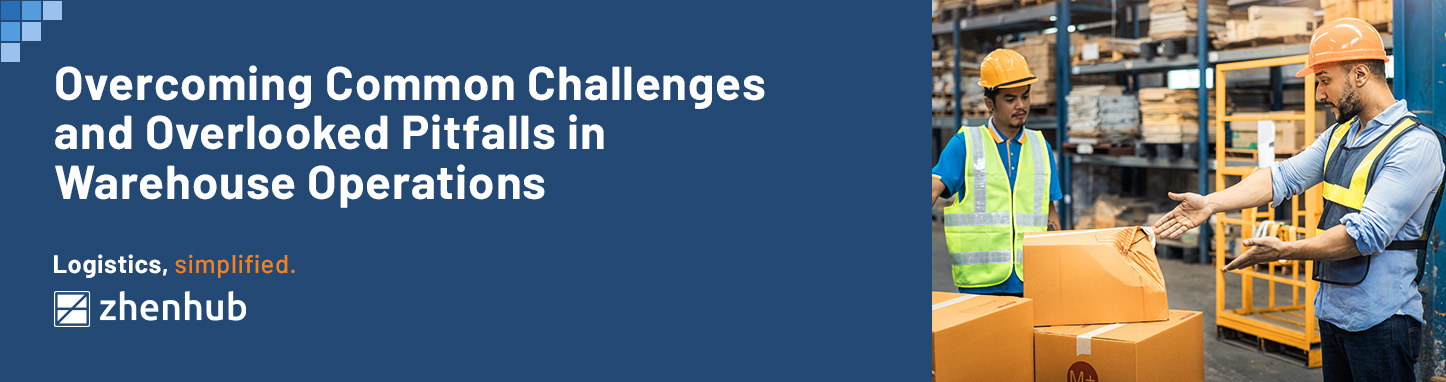
Overcoming Common Challenges and Overlooked Pitfalls in Warehouse Operations
Time to read: 7 minutes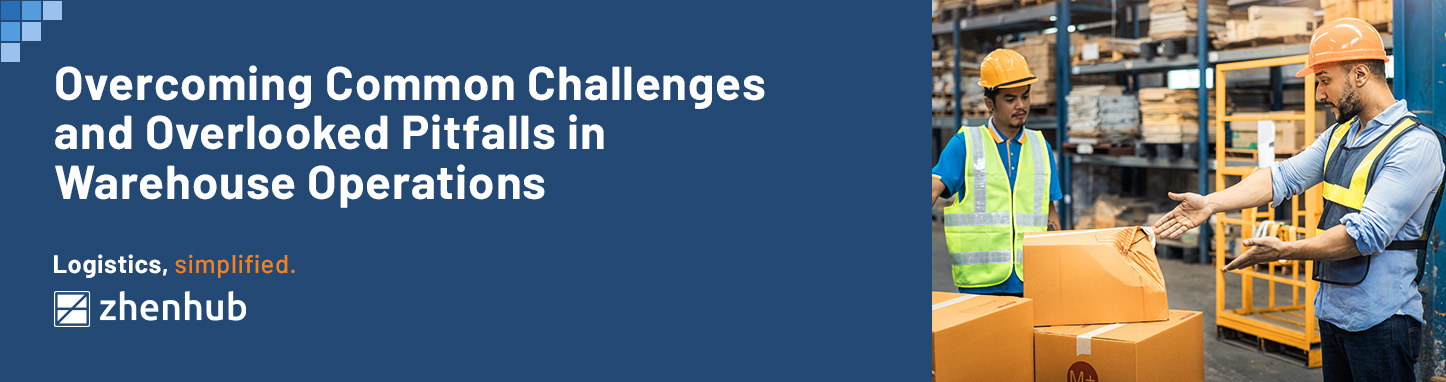
Warehouse management in the digital age comes with many exciting advantages for online merchants. But these opportunities also come with new challenges.
Warehouse management system (WMS) software and other technological advancements have made tracking shipping containers and connecting warehouses with logistics networks easier. However, common challenges in warehouse operations, like labor costs and space constraints, are still significant concerns for many logistics teams.
A warehouse is a complex ecosystem where many systems interact to deliver excellent customer service. Issues with warehouse management are roadblocks to the effectiveness and productivity of warehouses. Problems in the warehouse can negatively affect the entire warehouse’s workflow.
The most effective approach to guaranteeing sustainability and longevity for your warehouse is to directly address typical warehouse management obstacles. Recent events, such as the COVID-19 pandemic, have forced warehouses to adjust their business models to remain profitable while completing client orders.
Warehouse managers must always be on top of everything and ahead of warehousing obstacles. Their responsibilities include managing staff effectively, optimizing available warehouse space, and adjusting to seasonal demands and other concerns.
Nearly eighty-two percent (82%) of customers are concerned that supply chain disruptions, such as delivery delays, can severely affect their way of life. That’s why warehouse management is crucial to the supply chain and vital to the transportation and logistics sector.
With the rise of social commerce, two-thirds of global consumers expect to receive their items within 24 hours, with four in ten expecting delivery in under two hours. Disappointment is inevitable when shipment delays cause problems for customers’ expectations.
If the wait lasts too long, dissatisfaction may grow into frustration, mainly if the company does nothing to let customers know about it. During the supply chain crisis of 2021-2022, 66% of customers were already aware of delays in the supply chain and were thus more understanding. Sometimes, all customers want is transparency from merchants on these delays.
Delays can prevent buyers from converting even when a merchant is entirely open. Long shipping times cause 22% of customers to abandon their carts. Eighty-four percent (84%) of consumers will not return to shop from an online store after just one poor delivery experience. Brand loyalty can only do so much to prevent your customers from leaving.
Understanding the Challenges in Warehouse Operations
Problems in the warehouse can impact the productivity, speed, and efficiency of a single warehouse process or the entire chain of related procedures. These mistakes are typically discovered just after the procedure has started or even after it has been finished.
By that point, it’s usually too late to undo the mistake or even mitigate the harm that has been done. If you’re familiar with the many difficulties affecting your warehouse operation, you can predict them and prevent damage before they begin.
Stockouts – Out of Stock: What Is It, Causes, Impacts, and How to Avoid? (cashflowinventory.com)
Poor Inventory Management and Incorrect Stock Counts
In retail warehouses, accurate inventory management is essential. Inaccurate stock counts and poorly handled inventory data can cause severe problems for warehouse management. Inaccurate data can impact everything from customer satisfaction to the effectiveness of the supply chain.
For instance, erroneous stock levels can lead to stockouts or overstocking, which would disrupt the retail supply chain. Using advanced warehouse processes that guarantee accurate data and real-time tracking is often the first step to optimizing inventory management.
Inefficient Warehouse Layouts
Efficient warehouse processes require a strategic location and effective layouts.
Messy floorplans can result in inefficient use of available space, which reduces operational effectiveness. For example, a poorly planned warehouse layout can result in longer pick times and higher labor costs.
Effective warehouse space management is the key to conquering this problem. Use layout concepts that optimize available space and make products flow easily.
Warehouse managers should think about putting in place warehouse solutions that offer insights about ideal layout techniques, such as where to put fast-moving items.
Unoptimized Labor Management
Efficient labor management is a key component of supply chain management strategy. Ineffective warehouse labor management can result in lower staff morale, higher operating expenses, and decreased productivity.
Challenges in warehouse operations include understaffing, poor facility safety, unclear task distribution, and lack of instruction. Warehouse managers need to implement comprehensive labor management techniques to overcome these problems.
Managers must balance labor needs with warehouse demands and optimize staff scheduling through warehousing software. Moreover, investing in employee training initiatives raises skill levels and boosts productivity.
By concentrating on effective labor management, retail warehouses can guarantee a more responsive and agile staff. It’s essential for satisfying the changing demands of your customers.
Lack of Quality Control
Ensuring quality control is crucial for upholding a warehouse’s integrity. A lack of strict quality control procedures in retail warehousing can result in faulty or unsuitable products being delivered. It can lead to damaged brand reputation and customer trust.
Implement strict quality control procedures and warehouse management systems that monitor product quality throughout the supply chain.
Constant education on quality standards for warehouse workers guarantees consistent quality of products. It’ll improve customer satisfaction and reinforce warehouse operation effectiveness.
Inability to Meet Customer Demands
Some warehouses struggle to adjust to the changing needs of a dynamic supply chain and varying seasonal demands.
Warehouse operations can be affected by stockouts or overstocking due to an inability to scale operations up or down as needed. Forecasting demand based on past performance and industry trends is a must-have for efficient warehouse management.
Make use of predictive analytics in warehouse management systems to forecast demand and prepare for any changes in advance.
Five Strategies to Deal with Challenges in Warehouse Operations
Customer satisfaction and operational effectiveness both depend on a seamless warehousing procedure. It will be challenging to remain competitive if you cannot deliver items in good condition and on time.
1. Implement a Warehouse Management System (WMS)
Automation is a significant technical improvement in warehouse management systems. Automation is used by WMS to optimize workflows, decreasing the need for manual labor and increasing productivity.
Automation technologies, like barcodes and RFIDs, optimize warehouse operations by identifying the best paths for picking, restocking, and inventory management.
It can also increase worker productivity by automating monotonous chores so they can concentrate on higher-value work.
2. Optimize Warehouse Layout
A well-planned layout enhances workflow, minimizes travel time, and supports effective inventory management, leading to increased productivity and reduced costs.
Consider appropriate storage solutions based on the different kinds of inventory and the number of items handled.
Effective inventory management is supported by maximizing space and easy access to storage units. Create a warehouse layout that will facilitate the efficient movement of goods from receipt to storage, picking, packaging, and shipment.
Set up workstations and storage spaces to reduce needless handling and moving. A well-thought-out flow design shortens trip times and improves overall productivity.
Create lanes and design traffic flow so that it is easier for employees and products to move freely.
Plan the warehouse’s layout with flexibility and future expansion in mind. Make room for future growth, inventory type modifications, and process improvements. A flexible warehouse layout can support long-term operational efficiency and changing company demands.
3. Streamline Order Fulfillment
Start by choosing the best picking method for your products. Typical methods of picking consist of:
Batch picking: Every order receives a packing list from the WMS, which groups client orders with related or nearby SKUs together. Inventory is gathered by a picker from many packing slips at once.
Zone picking: Usually employed by larger warehouses. It works by segmenting your warehouse into zones, each holding a specific set of items. Every zone has an order picker who sources items from inside that particular zone. After that, the parcel is handed to another zone for another pick, similar to an assembly line.
Wave picking: Workers at the warehouse also complete many orders at once. Packing slips are arranged according to SKU similarity, inventory zone, or delivery date. Throughout their shift, the worker then sources these goods in “waves.”
Efficient packing helps to minimize errors and ensure accuracy. Use automated packing solutions, consistent packing procedures, and appropriate packaging materials to improve speed and accuracy.
4. Invest in Employee Training
Investing in employee training helps you build a skilled workforce, cut down on mistakes, and improve overall warehouse efficiency.
Increased productivity, comprehensive safety procedures, and seamless operations are all made possible by well-trained staff.
Provide thorough training courses that include all of the fundamental skills needed in a warehouse, such as software usage, equipment operation, safety protocols, and inventory management.
Training programs must incorporate theoretical and practical elements so that everyone understands and applies concepts in actual situations.
You must also periodically assess the success of your training initiatives. Get employee input, evaluate their work, and track any modifications to operational metrics. Make adjustments to training programs and address any areas that need work by using this information.
5. Improve Communication
Increasing coordination, guaranteeing efficient processes, and attaining warehouse operational excellence all depend on improved communications.
Good communication techniques promote teamwork, reduce misunderstandings, and increase productivity in warehouse administration.
Establish dependable and transparent lines of communication throughout the warehouse, such as email, messaging applications, and intercom systems.
Ensure all team members are taught to use these channels and have access to them. Clear channels lower the possibility of miscommunications and enable prompt information exchange.
A smooth and effective supply chain depends on addressing challenges in warehouse operations.
Warehouse managers can satisfy client expectations while preserving operational efficiency by concentrating on effective warehouse management. Streamlined warehouse procedures and warehouse management software are the foundations for dealing with many warehouse challenges.
ZhenHub gives your business access to high-tech warehouses that bring your products closer to your customers. Sign up for access to our online logistics software dashboard. Contact our fulfillment experts for more information on our global network of warehouses.