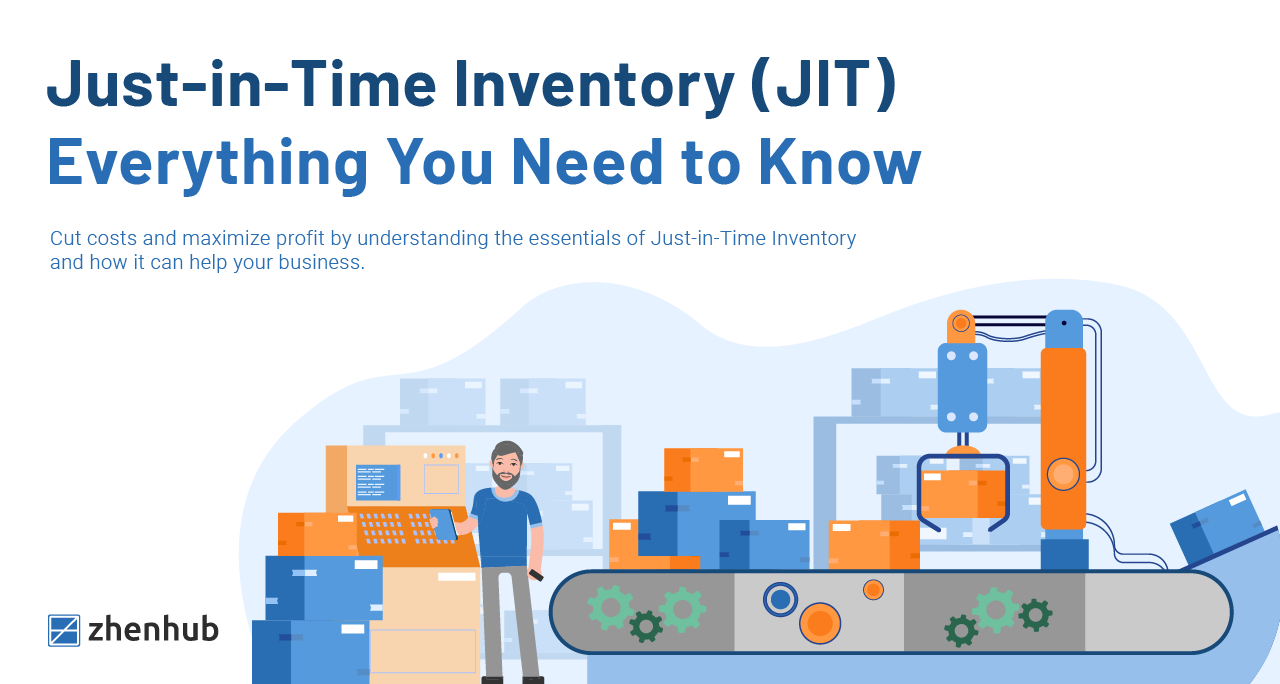
Just-in-Time Inventory (JIT): Everything You Need to Know
Time to read: 4 minutes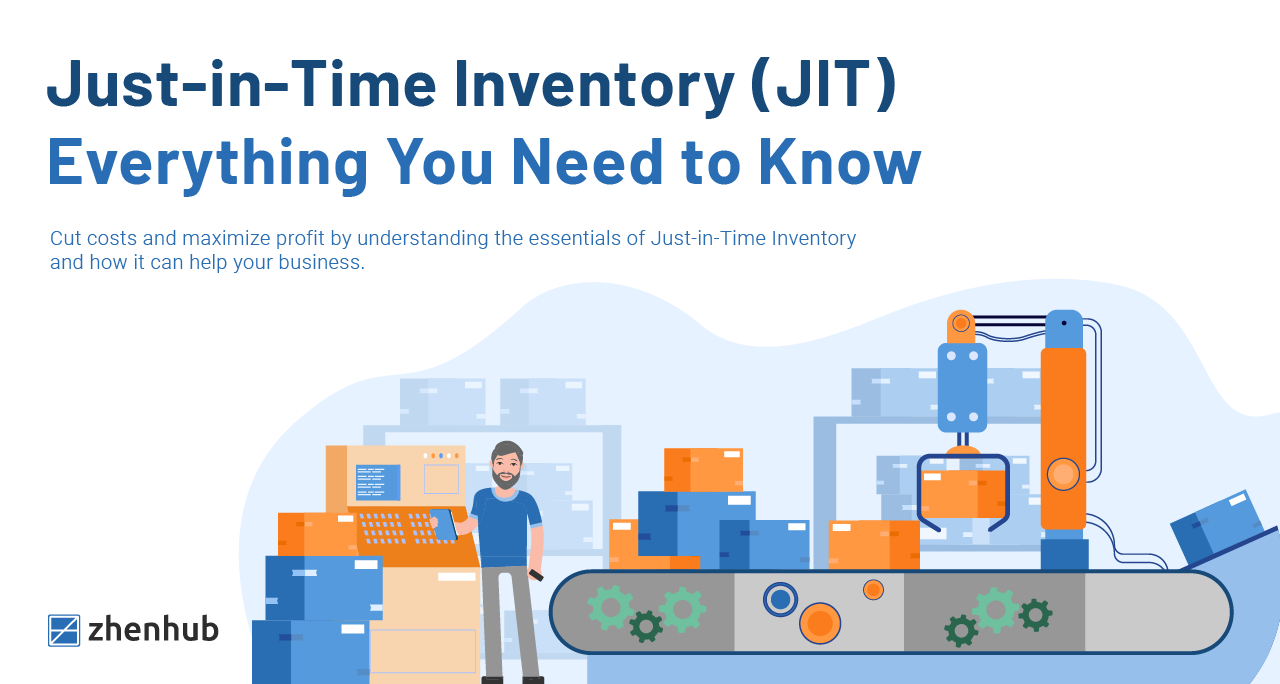
eCommerce will get bigger and bigger. More than 3 billion packages got delivered during the 2020 holidays, and billions of people made online transactions for several years. While these numbers are good for the global economy, it does pose several challenges, one of which is inventory management.
That’s why it’s essential to find the balance between overstocking and understocking requires a level of finesse. Too much inventory in stock can affect your bottom line; likewise, light inventory levels can affect order fulfillment time. For many businesses, online or otherwise, shifting to a Just-in-Time inventory management system improved their supply chain and reduced inventory management costs.
What is Just-in-Time Inventory?
Just-in-Time inventory management, or JIT, is a type of inventory management strategy that aims to reach maximum efficiency while lowering costs. It is a lean management framework that involves ordering and receiving the merchandise for order fulfillment only as needed.
Businesses that operate on a JIT inventory management strategy do not often carry plenty of products in stock. Because they do not hold safety stock, they invest in accurate demand forecasting for their products.
History of Just-in-Time Inventory
JIT has been around for years. It was developed in post-war Japan in the 1970s to solve the imbalance between the scarcity of resources, space, and cash and the increasing demands for consumer products. Automobile manufacturer Toyota originally developed JIT inventory management.
How Does Just-in-Time Inventory Work?
One of the goals of the JIT framework is to improve itself continually. As an example of that, early adopter Toyota, took 15 years to perfect their process.
The JIT process involves sourcing inventory or raw materials when an order comes in or when demand for a product is forecasted. “Pull triggers” determine when a new shipment is due to be shipped from the supplier or manufacturer. That said, the JIT inventory management cycle can come in many forms. However, below are the processes that most retailers do when they utilize practice this lean management strategy:
- Reviewing the Manufacturing Building Blocks
The first step in the JIT inventory management process involves reviewing all the key players that constitute the supply chain. This lean management framework operates on a small margin of error. For this reason, it is essential to take stock of everything integral in the order fulfillment process. This way, roadblocks are identified and managed before a problem crops up. This step is where companies identify crucial performance metrics. As organizations identify these KPIs, it also needs periodic review.
- Identifying the Pull Trigger
Like the JIT cycle, “pull triggers” varies from business to business. It is in the second step wherein companies identify these triggers. More than identification, it is crucial that all team members know the triggers to prevent delays in sourcing raw materials or read-to-ship products.
- Aligning with Credible Vendors
Vendors or suppliers are a crucial part of an efficient JIT inventory management flow. After all, they can make or break the entire process. Since there’s no safety stock, promptness in supplier delivery is paramount.
- Establishing Policies and Employee Roles
Just-in-Time inventory management requires all parts of the production cycle to be interconnected – this includes company employees and workers. Since employee tasks are interdependent of each other, it is essential to designate specific roles and expectations. Likewise, contingency policies should be in place to make up for any unforeseen workforce lapses.
- Reviewing and Refining the Process
Again, the beauty of the Just-in-time inventory process lies in its intent to grow and improve continually. As such, the last step in the cycle involves taking stock of the KPIs and reviewing it against the process flow’s actual performance.
The Kanban Method
At the heart of an efficient JIT inventory management process is the Kanban method. This scheduling system tracks the progress of production in a warehouse or factory environment. Kanban cards, which can be analog or digital, identify the inventory’s progress as it moves along the production process. The cards move as the stock progresses through the flow.
Advantages of JIT Inventory Management
Most eCommerce companies that adopt the JIT inventory management strategy do so to create a leaner operational model. It’s a cost-efficient solution, and there are several more benefits to JIT inventory management:
- Waste Management
One of the biggest draws of the Just-in-Time inventory management model is reducing waste in the overall supply chain process. Because warehouses do not hold slow-moving inventory, there’s less incidence of damaged products or rendered obsolete.
- Improved Productivity
Receiving inventory in bulk is not easy. There is more to receiving stock than loading and unloading a warehouse. With the JIT model, there is no longer a need to spend a lot of time receiving, sorting, and storing products for long periods. Since raw materials and ready-to-ship merchandise are procured as needed, expect faster turnaround times on manufactured items.
- Minimal Capital Investments
Overall, the Just-in-Time inventory management model is a money saver for eCommerce companies. It allows retailers to lower their inventory levels, thus reducing the capital needed to run the operation. Aside from a cost-effective capital funding solution, JIT also requires less labor force because products are made and prepared as needed.
Disadvantages of JIT Inventory Management
The Just-in-Time inventory management strategy provides tangible benefits to companies that adopt the model. However, like most inventory management frameworks, it has its drawbacks :
- Risk of Running Out of Stocks
The JIT management strategy forgoes the need for safety stocks. While this is great for keeping warehousing costs low, there is a risk of running out of supplies, thus failing to fulfill the demand. Failure to implement JIT properly can result in a loss in profit.
- Decreased Profit Margins
One of the drawbacks of sourcing inventory or raw materials as needed is the inability to shop around for the best pricing. When there is a surge in the pricing of merchandise, profit margins can suffer.
Key Takeaways
The Just-in-Time inventory management model is a great operational framework to transition to, but it requires a big deal of preparation. Again, while the cost-efficiency of this strategy is commendable, it leaves very little room for errors.
To transition to this new framework with ease, it is in your company’s best interest to partner with a reputable third-party logistics company. ZhenHub’s expertise can help you assess your supply chain and implement improvements to your business flow. Sign up today or request a quote to learn more about our technology-based solutions.