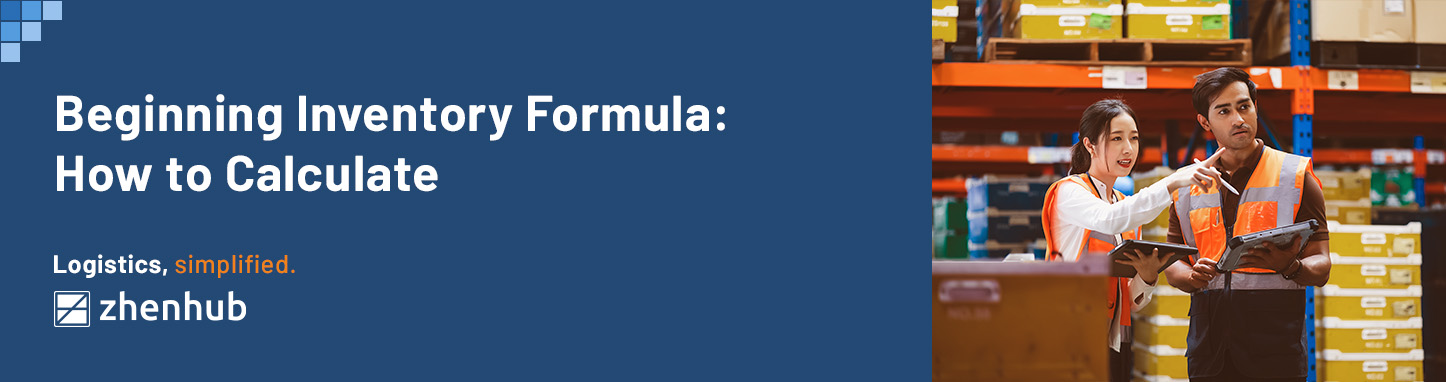
Beginning Inventory Formula: How to Calculate
Time to read: 6 minutes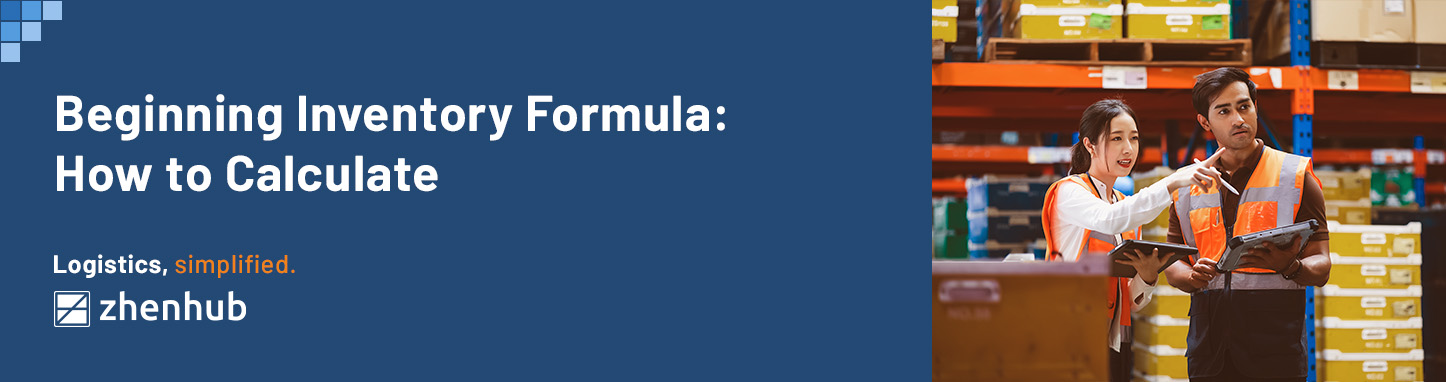
A company’s financial health and prospective profitability are understanding how much of a product or material is available at any one time and how much it is worth. Inventory is a valuable quantity that may be measured at many points during the accounting process. Beginning inventory is what your business needs to count when it starts an accounting period.
Beginning or opening inventory is the whole worth of a company’s available stock, prepared to be sold at the beginning of a new accounting period. The quantity of ending inventory from the previous accounting period should equal this amount.
Businesses must keep track of their beginning inventory to control stock levels, manage what’s on hand, and decide whether to buy more.
For manufacturers and retailers, their beginning inventory will vary. Beginning inventory for a manufacturer could consist of raw materials, commodities produced, and finished goods. However, a retailer’s initial stock consists of items customers can buy immediately.
The Importance of Beginning Inventory
Businesses tracking their beginning inventory levels can enjoy several benefits from doing so. The most crucial advantage is the ability to assess changes in inventory levels over time against a baseline provided by the beginning inventory count. This data can be used to evaluate the effectiveness of production operations and predict upcoming inventory requirements.
When evaluating the state of a business and its environment, it is crucial to remember that inventory level changes are only one aspect. It is impossible to decide on company environment changes solely based on inventory levels. To fully comprehend changing business environments, you must assess additional elements, including inventory levels, client demand changes, or the launch of new items.
Beginning inventory has a vital function in accounting as well. Balance sheets and other internal accounting records show the starting inventory value. Using this data lets you monitor your eCommerce company’s financial health. And with it, you can decide which investments to make. Beginning inventory may also be crucial in figuring out how much tax you owe.
Finally, beginning inventory is needed to determine the cost of goods sold (COGS). For many online merchants, COGS is a crucial measure as it gives information about the profitability of operations. It can be considered a gauge of how much it costs to generate its goods or services. The purchase cost incurred during the time is added to the beginning inventory value minus the ending inventory value. As a result, companies must have accurate and up-to-date beginning inventory data to produce accurate COGS data. This can subsequently be utilized to determine gross profit.
Knowing your initial inventory has many advantages. Consider the following:
Transparency
Your beginning inventory provides information on how much stock you have to deal with and how much you should order to prevent stockouts. Calculating how many products were sold over a specific period can also be done using the beginning inventory.
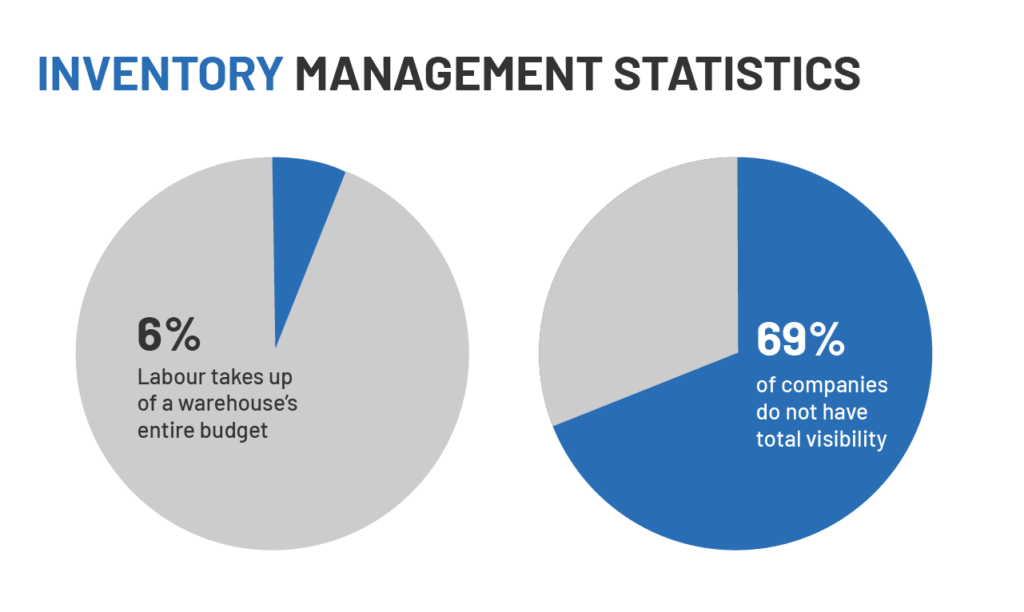
Inventory Management Statistics – Meteor Space
Better Forecasting
Knowing your inventory levels at the start of an accounting period is best. It’ll allow you to make more informed purchases based on anticipated demand for the remainder of that period. This is especially useful to prepare for seasonal demand before the peak season—the holidays.
Improved Inventory Management
Track the inventory at risk of becoming unsellable to detect better merchandise at risk of becoming “dead stock.” Additionally, you’ll be more aware of the status of your goods so you can prevent stockouts.
COGS Valuation
You need to be aware of your beginning inventory to determine COGS. Your COGS is the sum of your product sales over a given period, less your initial inventory. Knowing these two metrics can help you determine how much it will cost to manufacture and market your goods.
Calculating for Beginning Inventory
The formula for beginning inventory is as follows:
Beginning inventory = (COGS + ending inventory) – cost of inventory purchases
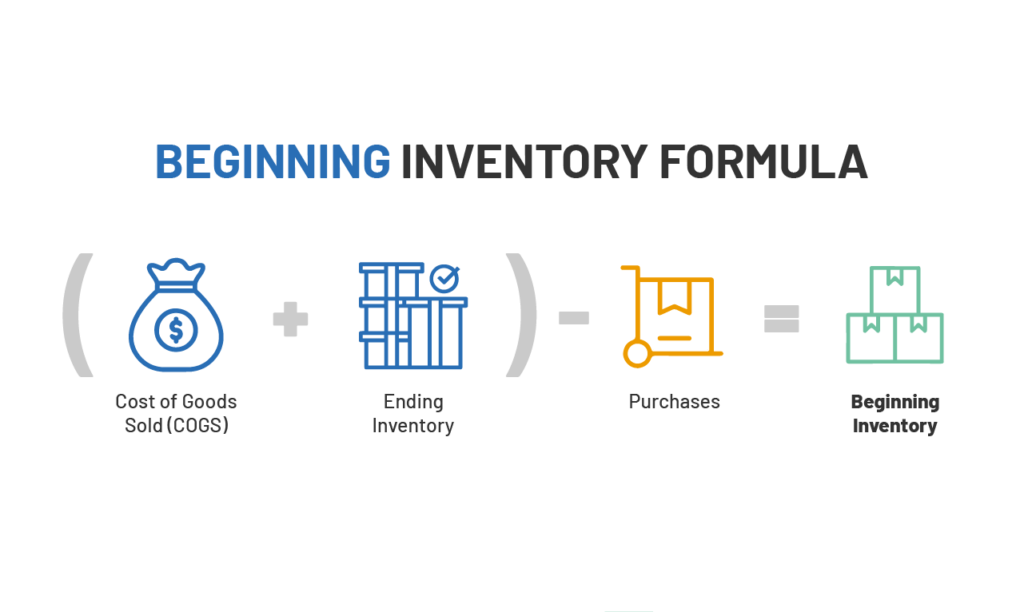
Beginning Inventory 101: Formula & How to Calculate (shipbob.com)
Before using the formula, we must understand each variable to compute for the beginning inventory.
Cost of Goods Sold
The cost of goods sold (COGS) reflects the amount spent on producing already sold things. It comprises the cost of labor, shipping, manufacturing, and raw materials.
The formula for determining the cost of goods sold is as follows:
COGS = (beginning inventory + purchases) – ending inventory
In other words, the amount you initially spent for the items you sold to clients during that time is the cost of goods sold.
COGS = Manufacturing Price x Quantity
Depending on your inventory system, the cost of items sold may vary. There are four standard popular inventory systems. Whichever your choice is, you must commit to it. You risk having inconsistent data in your reporting if you do not maintain continuity with the inventory system.
- Weighted Average Cost (WAC)
This valuation method, or the average cost method, works best for companies that ship items of comparable sizes. Its formula is as follows:
WAC = Cost of goods available for sale / Total units in inventory
- Specific Identification Method
Each item is tracked separately, leading to consistently precise data. This approach works well for companies whose goods come in various sizes and prices. This method has no set formula; you only have to tag every item with its purchase price and any subsequent costs until it is sold.
- First-in First-out (FIFO)
FIFO is a popular valuation technique because of its simplicity. As the name suggests, inventory that is produced first will be sold first. By using this technique, you may determine the overall value depending on the stock that you currently have.
- Last-in First-out (LIFO)
LIFO is a less popular inventory valuation technique since most merchants don’t sell their newest products first. There are, however, tax benefits to doing so. Higher COGS and a smaller balance of leftover inventory due to LIFO lead to lower taxes and increased cash flow.
Ending Inventory
You can determine your ending inventory using the accounting records from the previous financial period. In other words, your beginning Q2 inventory should be the same as your closing Q3 inventory.
If you’re calculating ending inventory for the first time, you’ll need to figure out how much new stock was bought and sold over a certain period.
Ending Inventory = Beginning Inventory + Net Purchases – COGS
Alternatively, you can get this value by multiplying the number of items and materials left in stock by their value.
Ending Inventory = Manufacturing Price x Remaining Quantity
With all these variables, you can now begin calculating your beginning inventory. First, you must determine your COGS by referencing the records from your previous accounting periods.
To better illustrate these computations, let’s use an example. Suppose you run an online business selling basketball shoes. You sold 200 pairs of a particular sneaker that cost $140. Our COGS will be $28,000.
$28,000 = 200 shoes x $140
By the accounting period’s end, you are left with 40 pairs of shoes. The ending inventory will be $5,600.
$5,600 = 40 shoes x $140
To accommodate demand, you purchase 120 new pairs of shoes at the start of a new accounting period. This gives us a total purchase value of $16,800.
$16,800 = 120 shoes, $140
With all the necessary data complete, we can now begin to compute for our beginning inventory:
Beginning Inventory = ($28,000 +$5,600) – $16,800
This gives us a beginning inventory of $16,800 at the start of a new accounting period.
According to the beginning inventory calculation, this is the amount of stock your eCommerce company should invest within the current accounting period. You may utilize this information to complete your balance sheets. Match it up with internal accounting records, and prepare for tax documentation.
A company can forecast future demand for its products by using historical inventory, seasonality, and sales data. Demand forecasting is the technique of estimating future sales.
Your business can answer how much inventory is required for stock, fulfilling future orders, and how frequently to restock. You can also better understand how sales trends change with demand forecasting. It can also be used to calculate projected sales and revenue totals. Demand forecasting assists an organization at a larger scale with budget planning, production scheduling, determining storage requirements, and product pricing strategies.
Understanding how to calculate your beginning inventory is just one step toward improving your eCommerce business’s financial stability and inventory system management. With ZhenHub, you can access all the necessary data to compute optimal inventory levels. Sync up to multiple online marketplaces and get real-time insights on stock movement. Sign-up on our website for free and discover all our logistics software solutions.