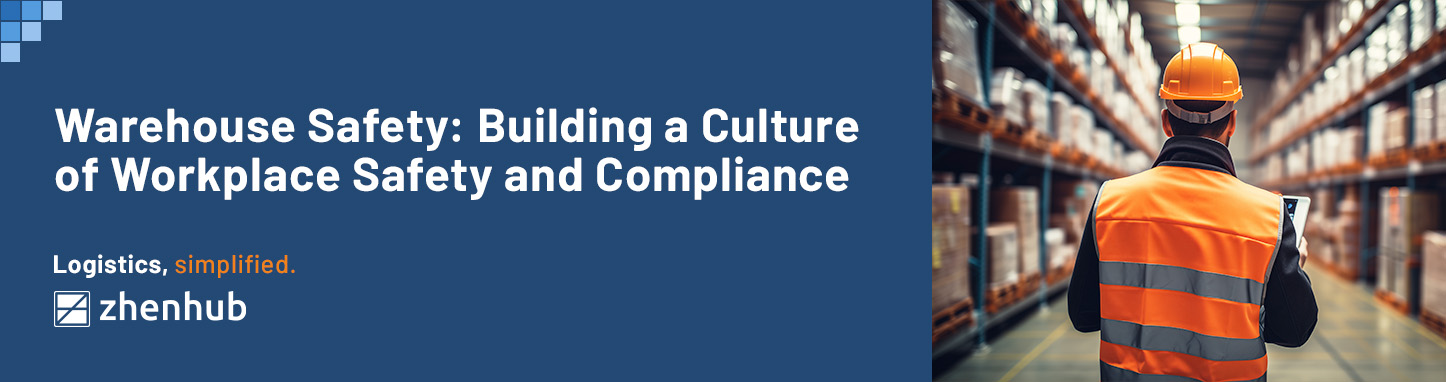
Warehouse Safety: Building a Culture of Workplace Safety and Compliance
Time to read: 6 minutes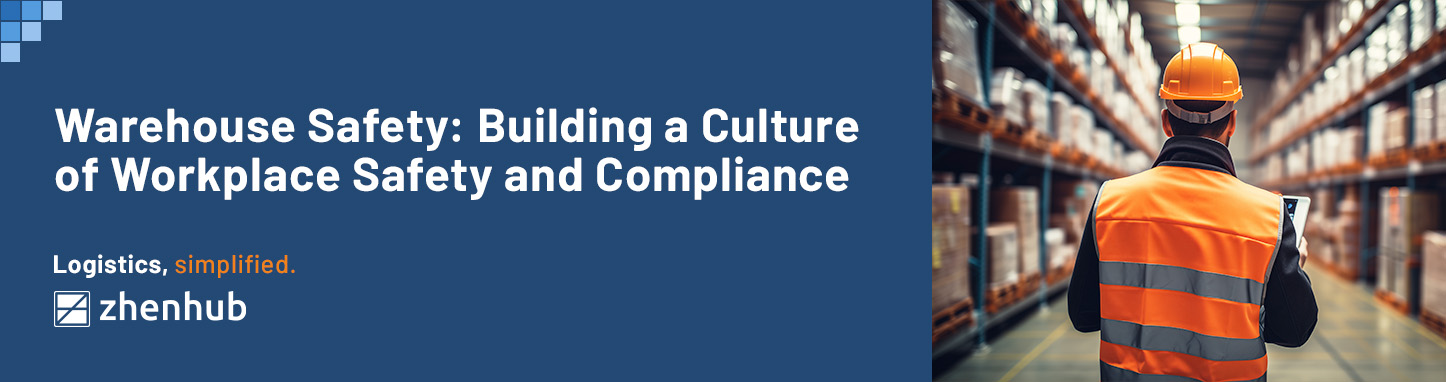
Warehouses, distribution, and fulfillment centers are busy, fast-paced environments with plenty of activity. These places rely on warehouse workers’ hard work to ensure that logistics and supply networks run smoothly. However, many potential workplace risks might endanger their health and safety.
Warehouse health and safety is an essential component of maintaining a safe and healthy workplace. Warehouses filled with heavy machinery, forklifts, and other equipment could become unsafe if safety is not prioritized. Businesses need to protect their workers and reduce the possibility of warehouse accidents and injuries by implementing efficient safety measures.
Working in a warehouse has its hazards. Typical warehouse risks and dangers may result in injuries and, in severe circumstances, death. Warehouse managers need to recognize and prepare for all potential safety hazards. According to the US Bureau of Labor Statistics, there are 16 average annual fatalities in the warehouse and storage industry in the United States. Five out of every 100 field workers report an accident or sickness.
For many organizations, warehouse health and safety are often overlooked. However, workplace accidents are costly and negatively impact business productivity. An extensive safety program can reduce or even eliminate the danger of accidents and injuries in your warehouse.
Human laborers still staff many warehouses in a supply chain. Your employees’ lives and safety are paramount to your firm’s reputation and success. Providing a worker-welfare-centric environment will make it appealing to individuals who want to work there.
Warehouse safety has a direct effect on efficiency and productivity as well. Workers won’t be as productive as they could be if they don’t feel comfortable or always avoid dangerous situations. Additionally, a high injury rate warehouse will have to pay higher insurance premiums, affecting profitability.
Warehouses must adhere to many safety standards. Businesses must follow specific minimum safety requirements set by the local governments while handling heavy machinery, doing repetitive tasks, or working at heights. Noncompliance with these requirements could result in severe fines and other consequences.
Tackling Major Warehouse Health and Safety Issues
Warehouse workers face potential hazards in their daily tasks, making safety compliance on the job site critical for their well-being. Understanding these potential warehouse hazards helps employers implement targeted safety measures to mitigate risks effectively.
Heavy Equipment Accidents
Forklifts and large pallets are examples of heavy warehouse equipment that can cause serious accidents and, occasionally, even fatalities. Employees can fall from an elevated platform, be struck by a forklift, or be trapped between the lift and the trailer. These accidents are typically caused by warehouse overcrowding, insufficient forklift safety instruction, or pure chance.
Slips, Trips, and Falls
Poor lighting, congested paths, uneven flooring, and slippery surfaces can lead to warehouse falls and slips. Bodily harm and even mental trauma could happen if these issues aren’t resolved quickly. For instance, a worker falling from a high platform might result in a potentially fatal accident, while slipping on a wet floor could cause a serious back injury.
Chemical Exposure
Hazardous chemicals, combustible materials, or poisonous gases are frequently handled and stored in warehouses. Exposure to these compounds can result in burns, chemical burns, respiratory disorders, and even long-term health concerns like cancer. Inadequate personal protective equipment (PPE), inappropriate handling, and inadequate ventilation might raise the risk of exposure-related diseases.
Heavy Lifting
Warehouse staff frequently handle heavy objects, which can cause musculoskeletal problems. Improper lifting techniques, insufficient training, and not using mechanical assistance can cause strains, sprains, hernias, and back problems. For example, failing to practice correct lifting procedures when moving a big box might strain an employee’s back, resulting in long-term injury to the spine.
Safety education and training give warehouse workers the know-how to foster a safety culture. Comprehensive warehouse health and safety protocols reduce the likelihood of accidents and injuries. Warehouse workers should be able to recognize any risks and understand the correct safety procedures. Using data in your warehouse can help you identify which parts of safety guidelines need the most attention.
Maintaining Warehouse Health and Safety: 7 Best Practices
Because workplace risks are unique to each type of organization, different safety regulations apply to various kinds of work. Nonetheless, employees in any warehouse are required to follow specific safety regulations.
Warehouses must adhere to regulations to guarantee that their projects are completed with the utmost professionalism and safety. Respecting industry rules and guidelines establishes safe procedures and reduces the risk of worker accidents.
4 types of warehouse safety signage that you should install (serviaplogistics.com)
1. Train employees in proper ergonomics
Warehouse workers perform a lot of heavy lifting. Therefore, they must receive training on safe lifting techniques to prevent injury to themselves and others. Your warehouse health and safety program should include ergonomics in the workplace. In addition to using lifting tables and lifting safely, good posture goes a long way. Teaching the proper techniques for manual lifting helps prevent injuries to the knees and back.
2. Proper fire safety
Your warehouse should have sprinklers, fire extinguishers, and alarms required by local safety codes. Having them in the warehouse is a great start, but it can all be wasted if workers aren’t taught how to use them properly. Conduct routine inspections and training sessions to ensure all staff know fire safety procedures.
3. Clear pathways
Good housekeeping goes a long way in the warehousing sector. Clear routes are a great technique for preventing trip-and-slip dangers. Injuries from trips and falls are standard daily, and warehouses are no exception.
Above all, maintaining clean aisles and passageways is essential to fire safety. Because of their design, warehouses are especially vulnerable to quickly spreading flames.
Consequently, every emergency exit must be well-marked and debris-free. It will guarantee that everyone can evacuate appropriately in an emergency.
If forklifts are used in your warehouse to carry items and machinery around, you should set up special lanes just for them. By constructing these routes, warehouse workers may avoid getting in the way of forklifts as they move around.
Hold a training session and publish educational maps and images everywhere to ensure that forklift drivers are familiar with these routes. Stickers with precise forklift routes should be placed on the ground to benefit everyone who works in the warehouse.
4. Use appropriate work attire and PPEs
They must wear suitable clothing to make your staff as secure as possible. Steel-toed boots protect the feet when operating near heavy machinery. A hard helmet protects the head from falling objects in a warehouse where products are stored in high piles. Wearing snug clothes prevents them from getting caught in between machinery.
While some warehouses have dress codes for employees, not all do. This means you’ll need to determine what clothes, accessories, and shoes will keep your employees safe while working.
5. Communication within the warehouse
Encouraging communication among warehouse employees can help ensure their safety and well-being. Effective communication can ensure that all employees in the warehouse are aware of safety-related procedures, regulations, and standards. Educating them can decrease the chance of accidents and health issues.
When developing safety plans, get feedback from warehouse workers about any safety issues they may have that you haven’t yet addressed. Giving staff members a forum to voice their opinions to managers can also improve workforce morale.
6. Optimized warehouse layout
Optimizing the warehouse layout is crucial for both worker productivity and safety. A logical flow to the warehouse’s layout can facilitate easier movement for personnel and equipment. Having a clear and organized warehouse layout may also assist staff in reacting quickly and effectively to emergencies. Moving products out faster means fulfilling client orders in less time.
7. Constant training sessions
Provide safety training sessions at a warehouse so all staff know the safety procedures. Hold training sessions focusing on warehouse areas, machinery and equipment practices, or fire and weather exercises.
Mandatory attendance helps with compliance and having a consistent understanding of warehouse health and safety procedures. A backup plan assures and lets your staff feel more secure at work.
It’s dangerous to work in a warehouse that doesn’t have any safety protocols. However, proper warehouse health and safety guidelines can significantly reduce these incidents. A basic understanding of frequent industrial injuries in warehouses, their prevention, and how to address them is beneficial.
Business leaders should prioritize warehouse health and safety by implementing appropriate training programs and conducting routine facility and equipment inspections. Abiding by all applicable laws and guidelines helps avoid fines and legal action. It also guarantees employee safety and reduces the risk of improper storage. A safer warehouse is a more efficient and sustainable warehouse.
ZhenHub’s logistics software assists with implementing comprehensive warehouse health and safety protocols. Our global network of fulfillment centers follows strict safety procedures. Have your products shipped out faster with warehouses that prioritize worker safety. Sign up and get access to our online dashboard. Contact our fulfillment experts and learn how to start going global.